گیربکس اکسترودر چیست؟
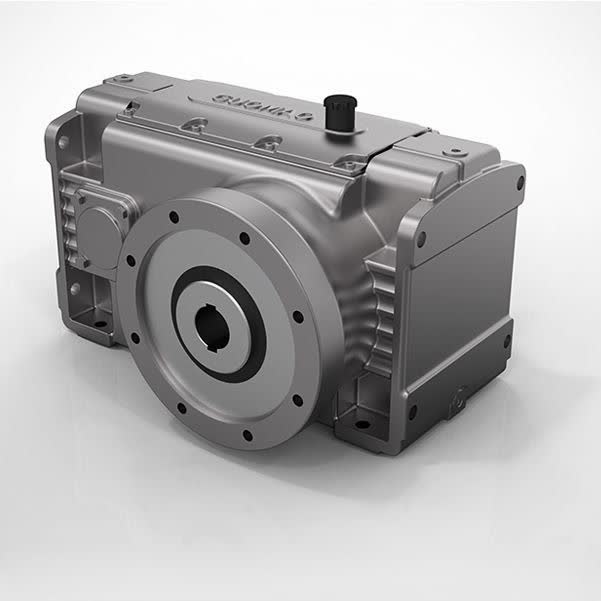
گیربکس اکسترودر (extruder gearboxes) جزء دسته گیربکسهای صنعتی میباشد. نوع گیربکس اکسترودر ویژگی خاصی داشته که آن را به یک قطعه خاص تبدیل کرده است.این گیربکس ها در هنگام حمل مواد، تحمل بار شعاعی، بار محوری، لحظهای و شوک را دارند. گیربکسهای صنعتی که برای تولید اکستروژن مورد استفاده قرار میگیرند، از این نوع گیربکسها هستند. در حقیقت عملکرد آنها به گونهای است که با استفاده از عملیات اکستروژن، مواد درون قالب را پرس میکند. پرس مواد توسط فرآیند اکستروژن، قطعه مورد نظر کاربر را تولید میکند. گیربکس اکسترودر جز دسته گیربکسهای شافت موازی هستند. به این نوع گیربکس، پارالل شافت نیز گفته میشود که در دسته گیربکسهای میانه قرار دارد. این نوع گیربکسها اجزای خاصی دارند. اجزای تشکیلدهنده بر کیفیت و عملکرد آنها تاثیرگذار است. انواع گیربکس اکسترودر extruder gearboxes در این مقاله با انواع این گیربکس ها آشنا میشویم.
گیربکس اکسترودر در دستگاه اکستروژن
Extrusion اکستروژن یک فرایند قالب گیری تولیدی است که شامل یک قالب پیششکل برای ایجاد اجسام با شکل و مشخصات خاص است. این فرایند برای ایجاد اشیا با مشخصات مقطع ثابت استفاده میشود. در هنگام کار، مواد تحت فشار از طریق یک قالب با سطح مقطع مورد نظر رانده میشوند، شکل آن ها تغییر میکند تا شکل قالب را منعکس کنند. محصولات Extrusion به طور کلی «اکسترودات» نامیده میشوند. از گیربکس های اکسترودر بواسطه توان، قدرت و گشتاور بالای خود برای تامین فشار تزریق مواد به درون قالب استفاده میشود. گشتاور بالای گیربکس اکسترودر سبب راحتی عملیات قالب گیری و ساخت پلاستیک میشود. در دستگاه اکسترودر از نوعی گیربکس صنعتی شافت موازی و یا گیربکس کرانویل بهینه شده استفاده میکنیم تا توان و گشتاور بالایی را برای تحمل بارهای محوری ماردون ایجاد کنیم. نحوه عملکرد دستگاه اکسترودر هم به این صورت است: نیروی تولید شده توسط الکتروموتور به گیربکس منتقل می شود، گیربکس اکسترودر دور را کاهش میدهد و گشتاور را بشدت افزایش میدهد و سبب چرخش ماردون و انتقال متریال به درون قالب میگردد. . جهت تامین و نگهداری گیربکس باتوجه به شرایط کار گیربکس در اکسترودر مشهد طراح به شما پیشنهاد میدهد واسکازین گیربکس را هر شش ماه تعویض نمایید غلضت واسکازین150می تواند گزینه مناسبی باشد حتماً از واسکازین های استاندارد استفاده شود واسکازین تسویه شده علیرغم قیمت پایین خسارات جدی به گیربکس وارد میکند همیشه از یک برند واسکازین استفاده کنیدفول روغن را حداقل بصورت ماهیانه چک کنبداگر بیشتر از دولیتر کم شده بود حتما کاسه نمد یاطاقان جلورابررسی کنیدسعی کنید از گیربکسی که رادیات خنک کننده دارد استفاده نماییدزیرا با پایین آمدن دمای روغن طول عمر گیربکس شما افزایش یافته واز خسارات جلوگیری میکند.
سیستم فیلتر هیدرولیک برای جلوگیری از ورود آلایندگی ها از دستگاه اکسترودر به خروجی مواد استفاده میشود ، این سیستم از یک صفحه فلزی مشبک مجهز به مکانیزم حرکتی هیدرولیکی ساخته شده که بدون نیاز به توقف دستگاه ، میتواند وظیفه تمیز کردن مذاب پلیمر را انجام دهد. در شیوه معمولی گرانولسازی و تولید محصولات پلیمری که فیلتر هیدرولیکی وجود ندارد، دستگاه هنگامی که فیلتر نیاز به تمیزکاری و پاکسازی دارد، میبایست کاملا خاموش شده و فعالیتش را ادامه ندهد، تا فیلتر از دستگاه که در قسمت مشخصی تعبیه میشود خارج شده و توسط اپراتور دستگاه ریکاوری و تمیز شود. این فعالیت زمان تقریبی دستگاه را میانگین ۱۰ الی ۲۰ دقیقه مختل میسازد. جهت رفع این مشکل دستگاه فیلتر هیدرولیک توسط ماشین سازی مشهد طراح طراحی و ساخته شده است ، این ابزار دارای یک جک هیدرولیکی میباشد که در برگیرنده صفحهات فیلتر است. اما به جای استفاده از تنها یک صفحه فیلتر، از دو فیلتر موازی استفاده میشود. زمانی که فیلتر نخست پر شده و نیاز به تمیزکاری داشته باشد، جک هیدرولیک فعال شده و فیلتر دوم را جابهجا میکند. با این وجود اپراتور زمانی که اکسترودر در حال کار کردن است، فیلتر نخست را تمیز نموده و دستگاه از فیلتر دوم استفاده میکند. زمانی که فیلتر دوم نیاز به تعویض داشته باشد، دستگاه از فیلتری که اپراتور تمیز نموده استفاده مینماید، همینطور شایان ذکر است که فیلتر ها فقط وظیفه فیلتراسیون را بر عهده ندارند، بلکه وجود فیلتر ها با شبکه بندی مناسب سبب ایجاد گرادیان فشار مناسب در قسمت خروجی مواد میگردد، این اثر باعث میشود که خروجی مواد از پایداری خروجی بیشتر و همگنی بیشتری برخوردار باشد، وجود این فشار ایجاد شده سبب مقاومت سیال و برگشت سیال به درون خود میشود، این رویداد سبب همزنی بهتر پلیمر درون کانال های ماردون میشود و در نهایت کیفیت محصول تولیدی را افزایش می دهد. زیاد شدن این مقاومت سبب عدم خروج مواد از دستگاه و کم شدن این مقاومت سبب ریپل زدن مواد خروجی و ناپایداری در تولید میشود بنابراین ، یک بازه کاری بسیار حساسی برای طراحی وجود دارد. محاسبه میزان افت فشار مناسب برای اینکار یکی از چالش های اساسی در صنعت پلیمر به خصوص بخش بازیافت پلیمر میباشد.
پیچیدگی فنی کلگی اکسترودر ناشی از چیست؟
از انجایی که وظیفه ی فشرده سازی نهایی و شکل دهی نهایی به عهده ی فیلتر ، مجهز به پمپ هیدرولیک ، می باشد. وقتی توری پر شود با سهولت با کمک پمپ هیدرولیک فیلتر جا بجا شده و فیلتر و توری جایگزین می شود تا تولید دستگاه متوقف نشود. توری پر شده به راحتی قابل تعویض و آماده سازی می باشد. بالاترین فشار در انتهای سیلندر و قسمت ورودی کلگی می باشد بنابراین باید از فولاد سخت شده استفاده کرد. پیدا کردن شکل مناسب برای کانال های بخش کلگی برای داشتن فشار از چالش های طراحی این قسمت میباشد، مقاومت این بخش باید به نحوی باشد که نه آنقدر کم باشد که مواد در خروجی دارای همگن سازی مناسب نباشد و ریپل بزند و نه باید فشار اینقدر زیاد باشد که سبب گیر کردن مواد و پس زدن از گازگیر دستگاه شود. به علت هندسه و ابعاد جدید سوراخ های فیلتر ها، این ادوات تنش های مکانیکی کمتری را تجربه میکنند و عمر کاری آنها به شدت افزایش میابد.همچنین هندسه باز طراحی شده این کانال ها سبب توزیع یکسان مواد در سوراخ های فیلتر ، عدم گیر کردن آنها و نتیجتا پخش شدن یکسان تنش های مکانیکی بر روی کل سطح فیلتر را بدنبال داشته که میزان تغییر شکل فیلتر را به حداقل مقدار خود میرساند.مشهد طراح جهت حل مشکل خرابی دریچه های هیدرولیک که عمدتاً مربوط به دیر تعویض شدن فیلتر میباشد سنسور فشار به. همراه آژیر خطر را پیشنهاد میدهد.